2025 מְחַבֵּר: Howard Calhoun | [email protected]. שונה לאחרונה: 2025-01-24 13:17
ראש כל מיזם, ללא קשר לתחום הפעילות, חולם שהרווחים יגדלו ועלויות הייצור יישארו ללא שינוי. מערכת "5S" בייצור (בגרסה האנגלית 5S), המבוססת רק על שימוש רציונלי ברזרבות פנימיות, עוזרת להשיג תוצאה זו.
מערכת זו לא נוצרה מאפס. משהו דומה בסוף המאה ה-19 הוצע על ידי האמריקאי פרדריק טיילור. ברוסיה עשה זאת המדען, המהפכן, הפילוסוף והאידיאולוג א.א. בוגדנוב, שפרסם ספר על עקרונות הניהול המדעי ב-1911. על בסיס ההוראות שנקבעו בו, הציגה ברית המועצות את ה- NOT, כלומר הארגון המדעי של העבודה. אבל המושלמת ביותר הייתה מערכת 5C שהוצעה על ידי המהנדס היפני Taiichi Ohno והוצגה על ידו במפעל טויוטה מוטור בייצור. מה זה ולמה השיטה היפנית הפכה כל כך פופולרית?
העובדה היא שהוא מבוסס על עיקרון פשוט שאינו דורש עלויות. זה מורכב מהבא - כל עובד, מהמנקה ועד המנהל, צריך לייעל את חלקו בתהליך העבודה הכולל ככל האפשר. הדבר מוביל לגידול ברווח הייצור בכללותו ולגידול בהכנסה של כלל עובדיו. כעת שרביט הצגת מערכת "5C" נאסף על ידי ארגונים בכל רחבי העולם, כולל רוסיה. במאמר זה ננסה לשכנע את הספקנים שהידע היפני באמת עובד, ובכל תחום פעילות.
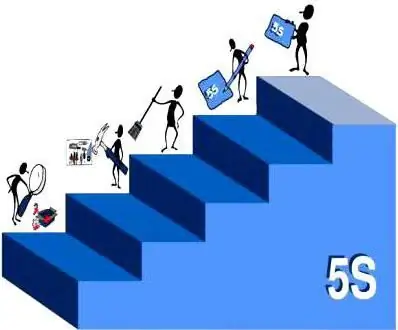
מערכת "5C" בייצור, מה זה
International 5S מייצג חמישה שלבים ("צעד" באנגלית צעד). כמה כלכלנים ומקדמים של גישה חדשה לעבודה מסבירים את השם על ידי חמש ההנחות היפניות המיושמות באופן עקבי במערכת ה-5S: seiri, seiton, seiso, seiketsu ו-shitsuke. עבורנו, ה-"5Cs" המקומיים שלנו קרובים ומובנים יותר - חמישה שלבים רצופים שצריך להשלים כדי להשיג את השגשוג של הייצור שלנו. זה:
1. מיין.
2. שומר על הסדר.
3. שומרים על ניקיון.
4. סטנדרטיזציה.
5. שיפור.
כפי שאתה יכול לראות, מערכת "5C" לא דורשת שום דבר על טבעי בייצור. אולי בגלל זה אפשר עדיין לפגוש חוסר אמון ויחס קל דעת כלפיה.
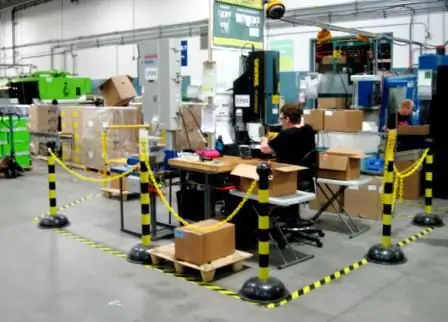
שלבי יצירת מערכת
טאייצ'י אונו היפני החכם, שבזכות הכנסת שיטותיו במפעל טויוטה הצליח להתרומם מ.מהנדס למנכ"ל, שם לב לכמה הפסדים מתרחשים עקב אי-עקביות ושכבות-על שונות. לדוגמה, כמה ברגים קטנים לא הוכנסו על המסוע בזמן, וכתוצאה מכך, כל הייצור הופסק. או להיפך, החלקים סופקו עם מרווח, הם התבררו כמיותרים, ובשל כך אחד העובדים נאלץ להחזיר אותם למחסן, מה שאומר בזבוז זמנם על עבודה ריקה. טאייצ'י אונו פיתח מושג שהוא כינה "בדיוק בזמן". כלומר, בדיוק כמה חלקים שצריך נמסרו כעת למסוע.
אפשר לתת דוגמאות אחרות. מערכת "5S" בייצור כללה גם את המושג "קנבאן", שפירושו ביפנית "סימן פרסום". Taiichi Ohno הציע להצמיד לכל חלק או כל כלי תג שנקרא "kanban", שבו ניתן כל המידע הדרוש על החלק או הכלי. בעיקרון, זה חל על כל דבר. למשל, לסחורות, תרופות, תיקיות במשרד. הקונספט השלישי עליו מבוססת מערכת ה-5S בייצור הוא המושג "kaizen", שמשמעותו שיפור מתמיד. כמו כן, הגו מושגים אחרים, אשר התאימו רק לתהליכי ייצור מיוחדים ביותר. במאמר זה לא נשקול אותם. כתוצאה מכל החידושים שנבדקו בפועל, נוצרו 5 שלבים המתאימים לכל ייצור. בואו ננתח אותם בפירוט.
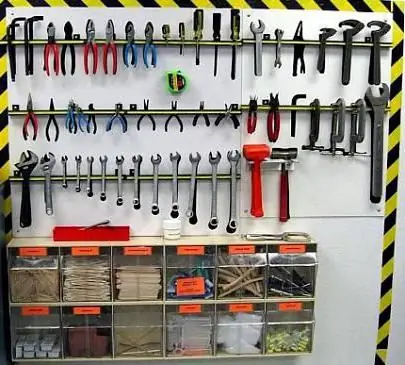
מיון
לרבים מאתנו יש פריטים על שולחן העבודה שלנו, בבעצם אין צורך. למשל, טפסים ישנים, קבצים שאינם בשימוש, טיוטות חישובים, מפית שעליה היה כוס קפה. ובין הכאוס הזה עשויים להיות הקבצים או המסמכים הדרושים. העקרונות הבסיסיים של מערכת "5S" כרוכים באופטימיזציה של זרימת העבודה שלך, כלומר, לוודא שהזמן לא יתבזבז בחיפוש אחר הדברים הנכונים בין ההריסות של המיותר. זה מיון. כלומר, במקום העבודה (ליד המכונה, על השולחן, בבית המלאכה - בכל מקום), כל הפריטים מונחים בשתי ערימות - ההכרחי והמיותר, שיש להיפטר מהם. יתר על כן, כל מה שאתה צריך מפורק לערימות הבאות: "בשימוש לעתים קרובות ומתמיד", "בשימוש לעתים רחוקות", "כמעט לא בשימוש". זה משלים את המיון.
שמירה על הסדר
אם רק תפרק את הפריטים, לא יהיה טעם. יש צורך לסדר את הפריטים הללו (כלים, מסמכים) בסדר כך שמה שמשתמשים בו כל הזמן ולעתים קרובות נמצא באופק, או כדי שניתן יהיה לקחת אותו במהירות ולהחזיר אותו בקלות. מה שמשתמשים בו לעתים רחוקות אפשר לשלוח לאנשהו בקופסה, אבל יש לצרף אליו תג קנבן כדי שאחרי זמן מה ניתן יהיה למצוא אותו בקלות ובדייקנות. כפי שניתן לראות, מערכת 5S במקום העבודה מתחילה בשלבים הפשוטים ביותר, אך למעשה היא מתבררת כיעילה מאוד. וחוץ מזה, זה משפר את מצב הרוח והרצון לעבוד.
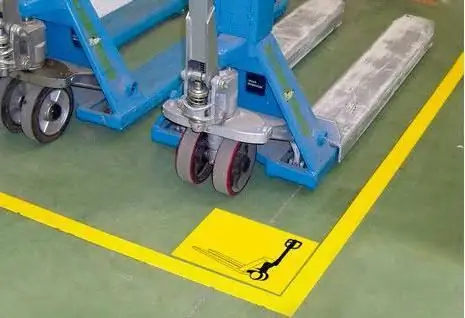
שמירה על ניקיון
השלב השלישי הזה הוא ההגיוני ביותר עבור רבים. מלמדים אותנו להיות נקיים מילדות. עלבייצור, זה גם הכרחי, ולא רק השולחנות של עובדי משרדים או ארונות במכוני קייטרינג, אלא גם מכונות, חדרי שירות של מנקים צריכים להיות נקיים. ביפן העובדים דואגים היטב למקומות העבודה שלהם, מנקים אותם שלוש פעמים ביום - בבוקר לפני העבודה, בצהריים ובערב, בסוף יום העבודה. בנוסף, המפעלים שלהם הכניסו סימון מיוחד של אזורים המאפשרים להם לשמור על סדר בייצור, כלומר אזורים של מוצרים מוגמרים, אחסון חלקים מסוימים וכן הלאה מסומנים בצבעים שונים.
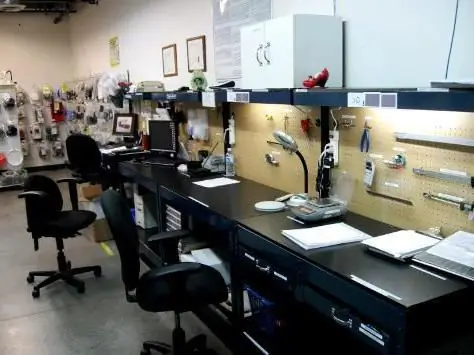
סטנדרטיזציה
עקרונות הסטנדרטיזציה הומצאו על ידי Taiichi Ohno. הם נמצאים בשימוש נרחב גם על ידי מערכת 5S המודרנית. ניהול הייצור, הודות לסטנדרטיזציה, מקבל כלי נפלא לשליטה בכל התהליכים. כתוצאה מכך, הסיבות לעיכובים מלוח הזמנים מתבטלות במהירות ומתוקנות שגיאות המובילות לשחרור מוצרים באיכות נמוכה. במפעל טויוטה מוטור נראתה התקינה כך: מנהלי עבודה ערכו תוכניות עבודה יומיות, הנחיות מדויקות פורסמו במקום העבודה, ובתום יום העבודה בדקו עובדים מיוחדים אילו חריגות מהתכנית התרחשו במהלך היום ומדוע. זהו הכלל הבסיסי של התקינה, כלומר הנחיות מדויקות, תוכניות עבודה ובקרה על יישומן. כעת ארגונים רבים, למשל, מפעלי ENSTO באסטוניה, מציגים מערכת בונוסים לעובדים העומדים בקפדנות בהוראות מערכת 5C ועל בסיס זה מגדילים את הפרודוקטיביות שלהם, אשרמהווה תמריץ נהדר לאמץ את המערכת הזו כדרך חיים.
שיפור
השלב החמישי, שמשלים את מערכת ה-"5S" בייצור, מבוסס על הרעיון של kaizen. המשמעות היא שכל העובדים, ללא קשר לתפקידם, צריכים לשאוף לשיפור תהליך העבודה בתחום המופקד עליהם. המהות הפילוסופית של קייזן היא שכל החיים שלנו משתפרים מיום ליום, ומכיוון שעבודה היא חלק מהחיים, היא לא צריכה להתרחק גם משיפורים.
תחום הפעילות כאן רחב, כי לשלמות אין גבולות. לפי התפיסות של היפנים, העובדים עצמם צריכים לרצות לשפר את תהליך הייצור שלהם, ללא הוראות או כפייה. כעת ארגונים רבים בונים צוותים של עובדים שעוקבים אחר איכות המוצר, מלמדים את החוויה החיובית שלהם לאחרים ועוזרים להשיג מצוינות.
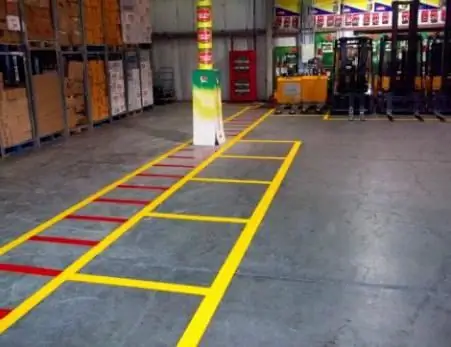
טעויות בסיסיות
כדי שמערכת "5C" תתחיל לעבוד, לא מספיק לארגן אותה או להעסיק עובדים שיכריחו את עמיתיהם ליישם אותה. חשוב שאנשים יבינו את התועלת של החידוש הזה ויקבלו אותו כאורח חיים. הכנסת מערכת ה-"5S" ברוסיה לייצור מתמודדת עם קשיים דווקא בגלל המנטליות הרוסית שלנו שונה מזו היפנית. רבות מההפקות שלנו מאופיינות בתכונות הבאות:
1. עובדים, במיוחד אם אין תמריצים עבורם, אינם מבקשים להגדיל את רווחי המיזם. הם שואלים,למה לנסות לעשות את הבוס אפילו יותר עשיר אם כבר יש לו הכל.
2. המנהיגים עצמם אינם מעוניינים בהכנסת מערכת "5S", כי הם לא רואים את כדאיות בכך.
3. הנחיות רבות "למטה מלמעלה" רגילים לבצע רק עבור "תקתק". ביפן יש יחס שונה לחלוטין לעבודתם. למשל, אותו טאייצ'י אונו, שהציג את מערכת ה-"5S", לא חשב על רווח אישי, אלא על התועלת של החברה שבה הוא היה רק מהנדס.
4. בארגונים רבים, מערכת 5S מוצגת בכוח. ייצור רזה, המרמז על ביטול הפסדים מכל הסוגים (זמן עבודה, חומרי גלם, עובדים טובים, מוטיבציה ואינדיקטורים נוספים), לא עובד, שכן העובדים מתחילים להתנגד לחידושים ברמה התת מודע, מה שבסופו של דבר מצמצם את כל המאמצים לאפס.
5. מנהלים המטמיעים את המערכת אינם מבינים עד הסוף את מהותה, מה שגורם לכשלים בתהליכי ייצור מבוססים.
6. הסטנדרטיזציה מתפתחת לרוב לבירוקרטיה, מעשה טוב מגודל עם הוראות והנחיות שרק מפריעות לעבודה.
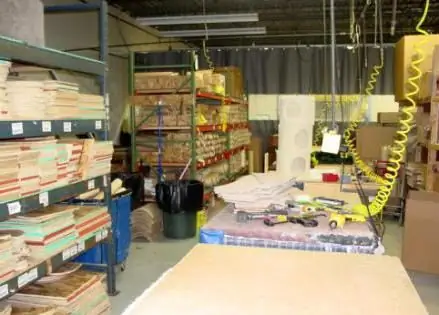
ביקורות
רוסים שהציגו את מערכת "5S" בייצור, המשוב על החידוש הזה הוא מאוד מעורפל. יתרונות מודגשים:
- טוב יותר להיות במקום העבודה;
- אל תסיח את דעתו מהעבודה עם דברים קטנים מיותרים;
- זרימת עבודה ברורה יותר;
- העייפות ירדה בסוף המשמרת;
- גדל מעטמשכורת על ידי הגדלת פריון העבודה;
- פציעות בעבודה ירד.
חסרונות שצוינו:
- בעת מיון, הם מאלצים לזרוק הכל;
- סטנדרטיזציה הובילה לעלייה בבירוקרטיה;
- הכנסת מערכת "5C" לא החריפה את הבעיות בכל תחומי הארגון;
- הצבת מערכת ה-5S במקום הראשון האפילה על נושאים חשובים כמו המחסור בחלקי חילוף.
מוּמלָץ:
מערכת "Rapida": תיאור, תכונות וסקירות
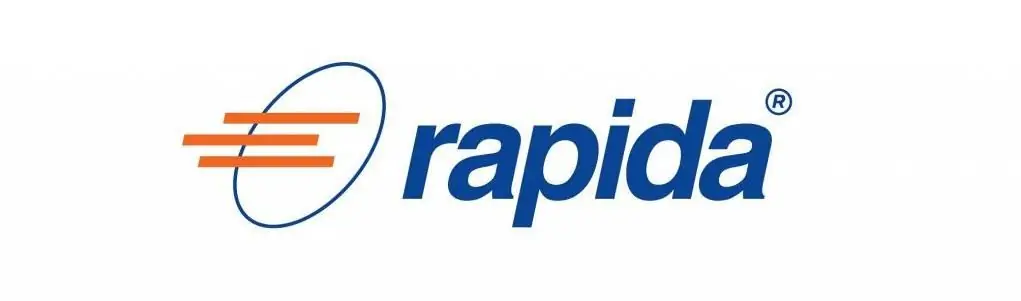
מערכת התשלומים "Rapida" היא שירות אוניברסלי. שירותיה מתאימים הן למשתמשים רגילים והן לבעלי עסקים. שקול את תכונות הפלטפורמה וכיצד מתבצע הליך הרישום והזיהוי של לקוחות
עקרונות בסיסיים של הלוואות: תיאור, תכונות ודרישות
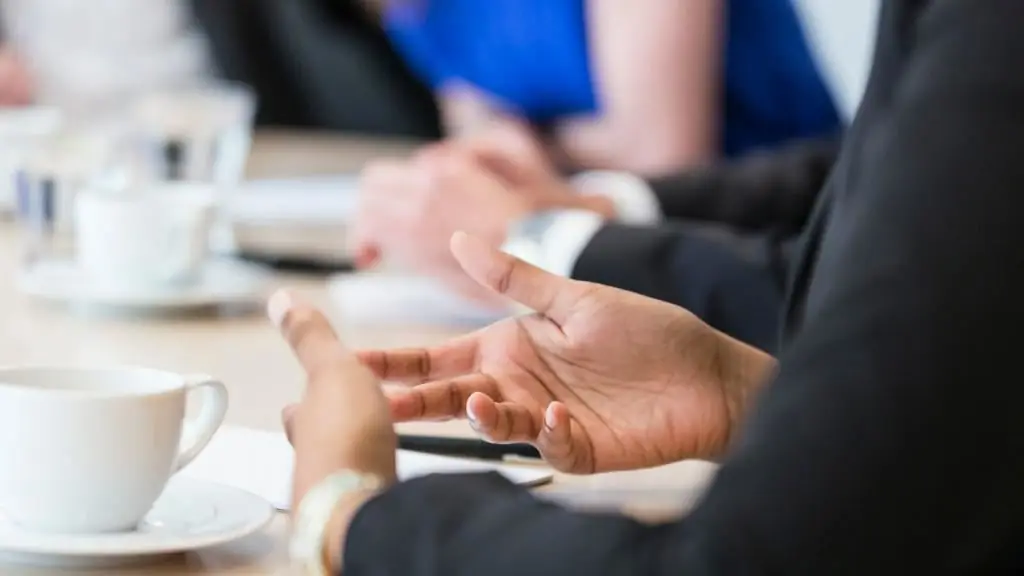
בתקופתנו הקשה, אנשים סובלים לעתים קרובות מבעיות כלכליות. אחד הפתרונות הטובים ביותר במצב זה הוא הלוואה. בררו מהם עקרונות ההלוואות והאם אתם עומדים בקריטריונים ללווה למופת
עקרונות בניית מערכת מס. מערכת המס של הפדרציה הרוסית
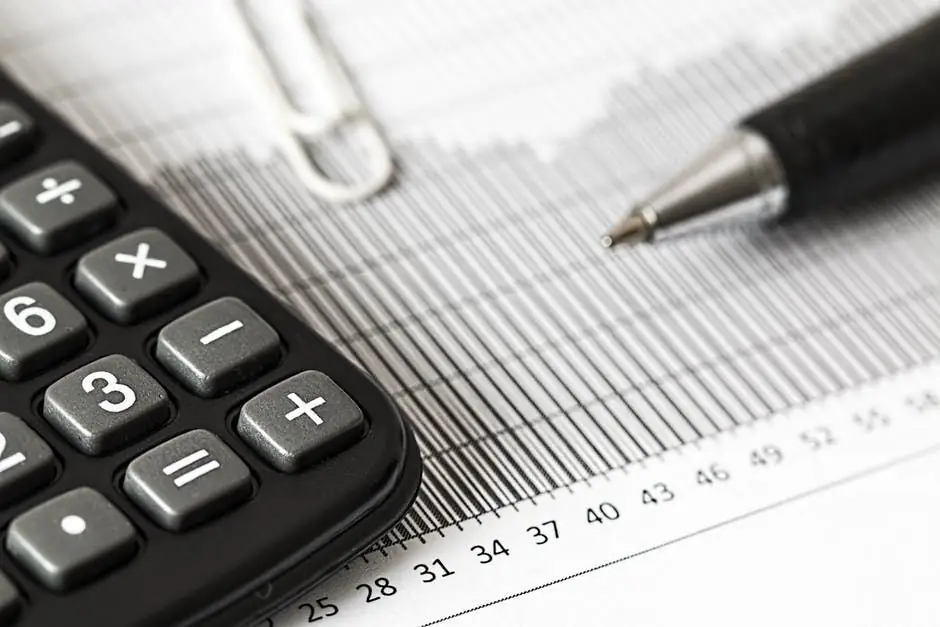
במערכת המיסוי, כל אחד ממרכיביו - המשלם (ישות משפטית או יחיד) מחויב בתשלום דמי שכירות או מס. מאמר זה יבחן את העקרונות של בניית מערכת מס או כמה דוגמאות שיש ליישם ביחס לנישומים ולמדינה
מערכת מחזור - תיאור, תכונות התקנה וסקירות
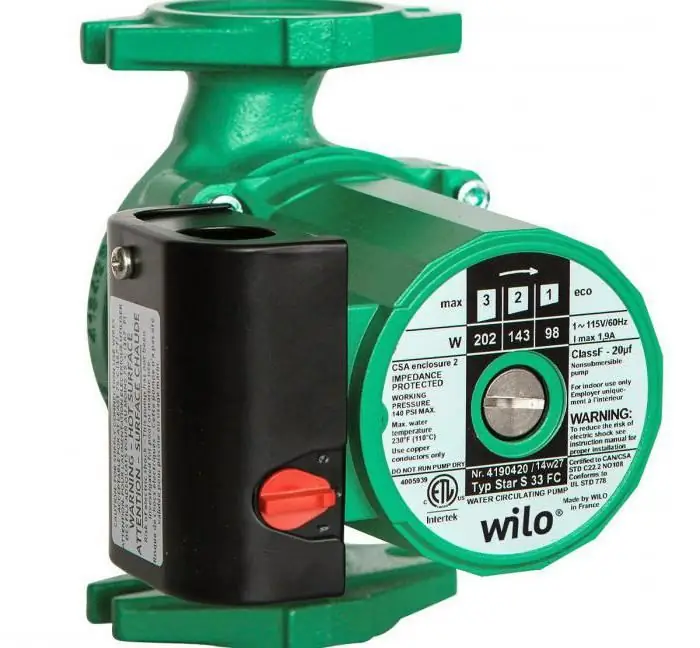
המאמר מוקדש למערכות תפוצה. המכשיר של מערכת זו נשקל, כמו גם עבודת התקנה על התקנת המשאבה וסקירות
מערכת טילים נגד מטוסים. מערכת טילים נגד מטוסים "איגלה". מערכת טילים נגד מטוסים "אוסה"
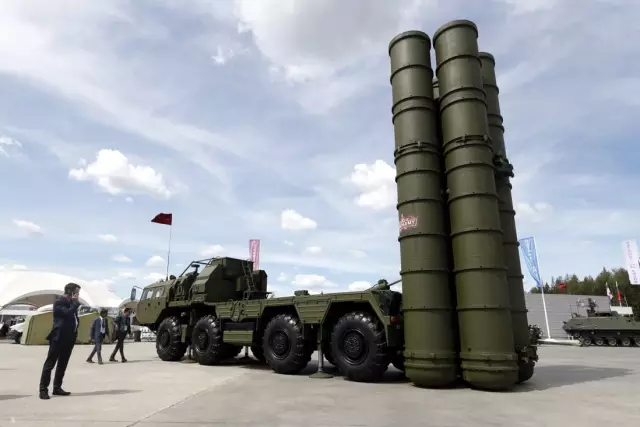
הצורך ליצור מערכות מיוחדות של טילים נגד מטוסים היה בשל במהלך מלחמת העולם השנייה, אך מדענים ואקדחנים ממדינות שונות החלו לגשת לנושא בפירוט רק בשנות ה-50. העובדה היא שעד אז פשוט לא היו אמצעים לשלוט בטילי יירוט